Spis treści
- Tradycyjny beton a ekologia
- Pojęcie betonu niskoemisyjnego
- Zalety i wady betonu niskoemisyjnego
- Paliwa alternatywne w przemyśle cementowym
- Uzupełniające materiały cementowe (SCM)
- Cementy aktywowane alkaliami
- Cement portlandzki bogaty w belit
- Cement sulfoglinianowy wapnia
- Cement na bazie magnezu
- Karbonatyzowany cement krzemianowo-wapniowy
- Zrównoważony rozwój w przemyśle cementowym
Tradycyjny beton a ekologia
Beton zyskał status przydatności użytkowej dzięki właściwościom mechanicznym i relatywnie niskiej cenie, zwłaszcza w porównaniu z innymi dostępnymi materiałami. Wywiera on jednak ogromny wpływ na środowisko, ponieważ zużywa duże ilości zasobów naturalnych, a jego produkcja uwalnia ok. 1 t CO2 na każdą tonę wyprodukowanego cementu portlandzkiego.
Proces wytwarzania cementu portlandzkiego, który nadaje betonowi jego wyjątkowe właściwości strukturalne, jest niezwykle intensywny pod względem emisji. Chociaż w większości stanowi zazwyczaj nie więcej niż 15% objętości betonu, odpowiada za ok. 80% emisji CO2 wynikającego z produkcji tego materiału.
Przemysł budowlany poszukuje zatem technologii mających na celu ograniczenie emisji CO2, w tym stosowanie surowców pochodzących z recyklingu, paliw niskoemisyjnych czy kombinacji materiałów o niskiej zawartości węgla.
Wiele z nowatorskich rozwiązań powoli zaczyna zyskiwać na znaczeniu w przemyśle budowlanym, wciąż jednak pozostaje spora liczba innowacji, które są jeszcze niezbyt zaawansowane technologicznie i niewystarczająco dobrze zbadane, ale mogłyby zostać wdrożone na szerszą skalę.
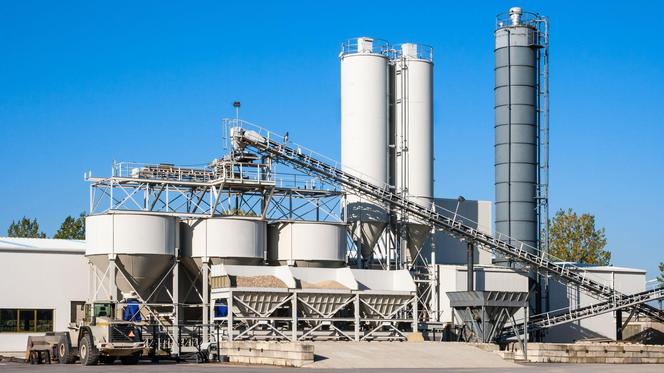
i
Pojęcie betonu niskoemisyjnego
Betonem niskoemisyjnym nazywa się materiał wytwarzany z cementu o niskim śladzie węglowym, który spełnia wymogi zrównoważonego budownictwa. Pojęcie to odnosi się nie tylko do pojedynczego produktu, lecz także do spektrum podejść, które samodzielnie lub w połączeniu mają na celu zmniejszenie emisji gazów cieplarnianych w porównaniu z konwencjonalnymi materiałami.
Koncepcja betonu niskoemisyjnego, która pojawiła się już pod koniec ubiegłego wieku, początkowo miała na celu całkowite lub częściowe zastąpienie składników zwykłego betonu odpadami i materiałami pochodzącymi z recyklingu. Z czasem została rozszerzona o nanomateriały, które mogą poprawić właściwości mechaniczne betonu, a w rezultacie jego trwałość w całym cyklu życia.
Betony określane mianem niskoemisyjnych powinny charakteryzować się przede wszystkim:
- identyczną bądź lepszą wytrzymałością i trwałością w porównaniu do betonu konwencjonalnego;
- intensywnym wykorzystaniem materiałów odpadowych i z odzysku;
- niskoenergetycznymi metodami wykonania.
Obniżenie śladu węglowego związanego z produkcją cementu – oprócz ogromnego zużycia kruszyw i wody – stanowi najważniejsze wyzwanie, z którym obecnie muszą się zmierzyć naukowcy i inżynierowie. Emisje CO2 powstają głównie podczas procesu produkcji cementu portlandzkiego i są przypisywane:
- spalaniu paliw kopalnych podczas procesu produkcyjnego w temperaturze ok. 1400°C;
- chemicznemu rozkładowi węglanu wapnia (CaCO3), który jest głównym składnikiem cementu, do wapna CaO (tlenek wapnia) i CO2.
Na szczęście na przestrzeni lat zidentyfikowano komponenty, które nie tylko przyczyniają się do niższej emisyjności, lecz także wpływają korzystnie na parametry techniczne betonu.
Na przykład popiół lotny skraca czas wiązania bez obniżania wytrzymałości i zapewnia lepszą urabialność betonu. Popiół z łusek ryżowych, jako dodatek do cementu, przyspiesza wiązanie i twardnienie zaczynów, zmniejsza nasiąkliwość betonu oraz poprawia właściwości wytrzymałościowe, w tym przede wszystkim wytrzymałość wczesną. Mielony granulowany żużel wielkopiecowy i popiół z odpadów komunalnych ograniczają emisję CO2 i zmniejszają ciepło hydratacji.
Dodatek szkła odpadowego (mielonej stłuczki szklanej) wpływa na lepszą wytrzymałość na ściskanie oraz poprawia odporność w wysokiej, jak i niskiej temperaturze. Popiół lotny, popiół z łusek ryżowych, pył krzemionkowy i inne popioły pucolanowe są wprowadzane jako zamienniki cementu, podczas gdy kruszywo z recyklingu to potencjalna alternatywa dla kruszywa konwencjonalnego. Mielony granulowany żużel wielkopiecowy, odpady szklane, tworzywa sztuczne oraz kilka produktów ubocznych rolnictwa i akwakultury stanowią obiecujące substytuty tradycyjnego cementu i kruszywa.
Wykorzystanie powyższych produktów nie jest jednak pozbawione wad, a decyzja o zastosowaniu któregokolwiek z nich zależy od:
- właściwości mechanicznych i chemicznych;
- dostępności;
- kosztów.
Beton niskoemisyjny może zawierać nie tylko składniki, które były wcześniej używane w przemyśle lub gospodarstwach rolnych.
Prace nad tymi materiałami uwzględniają również bardziej zaawansowane podejście nanotechnologiczne. Poprzez rozwój badań inżynieryjnych możliwe jest coraz lepsze poznanie chemicznych i fizycznych właściwości materiałów. Takie eksperymenty i odkrycia to początek wdrażania nowych rozwiązań w budownictwie, jak np. beton samonaprawialny czy ekospoiwa geopolimerowe, które mają na celu zmniejszenie ilości cementu portlandzkiego, a tym samym emisji CO2.
Za podstawowe narzędzie do badania nanostruktur i zrozumienia zachowania materiałów na poziomie atomów uznaje się metody symulacji dynamiki molekularnej. Obecnie są one wykorzystywane w zastosowaniach inżynierskich, do badania właściwości chemicznych i fizycznych cementu portlandzkiego oraz do opracowywania nowych materiałów, takich jak nanorurki węglowe w technologii zaczynów cementowych.
Przeczytaj również:
- Czy branża budowlana wdraża strategię ESG? Konieczna rewolucja na placu budowy
- Czy będziemy budować z betonu bez cementu? Co może zastąpić cement?
Koncepcja betonu niskoemisyjnego dotyczy wszystkich faz cyklu życia konstrukcji betonowych – od projektowania poprzez produkcję, proces budowy i eksploatację. Ponadto obejmuje wszystkie aspekty wydajności, tj. właściwości mechaniczne, odporność ogniową, wytrzymałość.
Jeśli chodzi o wymagania środowiskowe, konstrukcje wykonywane z betonu niskoemisyjnego powinny spełniać następujące warunki:
- zmniejszenie emisji CO2 o co najmniej 30%;
- zastosowanie kruszywa recyklingowego w ilości wagowej co najmniej 20%;
- wykorzystanie pozostałości produktów z przemysłu cementowego;
- zastąpienie paliw kopalnych w produkcji cementu o co najmniej 10%.
Zalety i wady betonu niskoemisyjnego
Do najważniejszych zalet betonu niskoemisyjnego można zaliczyć:
- relatywnie niski ślad węglowy;
- dobrą odporność termiczną i kwasową;
- możliwość uzyskania lepszej wytrzymałości na ściskanie i rozciąganie (w porównaniu z konwencjonalnym betonem);
- odpowiednią konsystencję mieszanki;
- możliwość dostosowania parametrów w zakresie wytrzymałości i trwałości;
- niższe ciepło hydratacji (mniejsze ryzyko powstawania rys na skutek skurczu plastycznego);
- zmniejszenie zużycia cementu portlandzkiego.
Co równie istotne, przygotowanie betonu niskoemisyjnego niewiele różni się od przygotowywania mieszanki tradycyjnej. Materiał ten wyróżnia szerokie zastosowanie. Nadaje się m.in. do budowy:
- ścian zewnętrznych i wewnętrznych;
- podjazdów;
- chodników,
- innych elementów konstrukcji (np. fundamentów, słupów i belek).
Betony niskoemisyjne można także wykorzystać w niestandardowych rozwiązaniach, w zależności od rodzaju mieszanki i przeznaczenia konstrukcji.
Materiał ten ma też jednak (w porównaniu do konwencjonalnego betonu) pewne ograniczenia, takie jak:
- krótszą żywotność;
- stosunkowo dużą absorpcję wody;
- obniżenie niektórych parametrów technicznych, w tym wytrzymałości na zginanie i ściskanie;
- konieczność dokładnego przetestowania i sprawdzenia właściwości przed wprowadzeniem do użytku na dużą skalę.
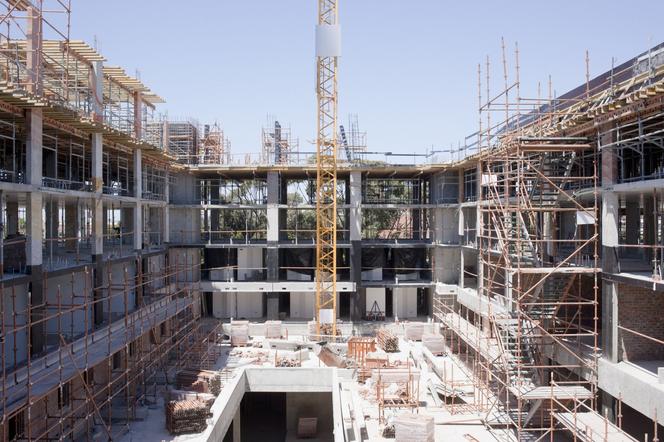
i
Paliwa alternatywne w przemyśle cementowym
Paliwem alternatywnym, wykorzystywanym przez przemysł cementowy, są głównie zużyte opony, osady ściekowe, pozostałości zwierzęce, odpady olejowe, pozostałości papierowe, tworzywa sztuczne czy tekstylia.
Wykazano, że biomasa może skutecznie ograniczać emisję CO2 o ok. 20–25% w porównaniu z węglem. Integracja związków nieorganicznych podczas spalania sprawia, że paliwa zastępcze najlepiej nadają się do redukcji emisji i uzyskania produktu klinkierowego o cechach korzystniejszych dla środowiska. Włączenie tych paliw do procesu pozwala też na optymalne dostosowanie profilu temperaturowego. W niektórych piecach cementowych realne jest uzyskanie 100% poziomu substytucji, ale w większości systemów jest to trudne z uwagi na lokalne warunki dotyczące gospodarki odpadowej.
Poza tym istnieją też pewne praktyczne ograniczenia, które polegają na tym, że właściwości chemiczne alternatywnych paliw różnią się od tych tradycyjnych. Na przykład podczas spalania zużytych opon w piecu cementowym wzrasta zawartość tlenku cynku. Powoduje to wprowadzanie różnych składników do klinkieru poprzez popioły, co skutkuje niższą jakością ostatecznego produktu cementowego, co objawia się np. krótszym czasem wiązania i mniejszą wytrzymałością.
Ponadto, aby wykorzystać paliwa niekopalne, przemysł cementowy musi uzyskać pozwolenie od organów ochrony środowiska; decyzja poprzedzona jest oceną środowiskową.
Uzupełniające materiały cementowe (SCM)
Dodatkowe materiały cementowe (ang. Supplementary Cementitious Materials, SCM) – ze względu na właściwości pucolanowe – mogą być stosowane jako wypełniacze. Zbudowane są z amorficznych glinokrzemianów, które reagują z nadmiarem wapna hydratyzowanego powstającego podczas hydratacji cementu, tworząc glinokrzemiany wapnia. Materiały cementowe SCM mogą mieć pochodzenie naturalne lub przemysłowe.
Pucolany naturalne
Naturalne pucolany są skałami piroklastycznymi (produktami wybuchu wulkanicznego) i nie wymagają wstępnej obróbki, aby zareagować z wodorotlenkiem wapnia. Ich aktywność pucolanowa wynika z dużej zawartości krzemionki. Typowymi przykładami minerałów krzemianowych są: kwarc, mika, piroksen i skaleń. W odróżnieniu od nich sztuczne pucolany, aby zareagowały z wodorotlenkiem wapnia, wymagają wcześniejszej aktywacji.
Pucolany sztuczne
Wśród sztucznych pucolanów znajdują się np. iły kalcynowane, w których aktywność pucolanowa zależy od rodzaju i ilości kalcynowanych minerałów, ilości zanieczyszczeń, sposobu aktywacji oraz pola powierzchni po kalcynacji. Spośród różnych typów najwyższą aktywność pucolanową ma kaolinit.
Chociaż kalcynowany kaolinit jest doskonałym kandydatem na uzupełniający materiał cementujący, wymóg obróbki wzbogacającej w celu wyeliminowania zanieczyszczeń podczas produkcji metakaolinu pochłania energię, wiążę się z wytwarzaniem odpadów i zwiększa koszty.
Przemysłowe SCM
Główne przemysłowe SCM to: żużel wielkopiecowy, popiół lotny oraz pył krzemionkowy (na mniejszą skalę).
Żużel wielkopiecowy jest produktem ubocznym przemysłu hutniczego, który po obróbce wielkopiecowej wymaga zeszklenia w celu uzyskania właściwości wiążących. Zawiera glinokrzemiany wapnia i magnezu oraz ma podwyższoną zawartość CaO. Żużel, z uwagi na niewystarczającą dostępność, nie jest w stanie całkowicie zastąpić tradycyjnego klinkieru.
Kolejny ważny materiał uzupełniający to popiół lotny, który powstaje podczas spalania w elektrowniach węglowych. Składa się głównie z tlenku krzemu, ale zawiera również znaczne ilości tlenków glinu i tlenku żelaza. Jest dostępny w większych ilościach niż żużel, ale ze względu na różnice w jakości, tylko ok. jedna trzecia może być wykorzystywana w przemyśle cementowym i betonowym.
Pył krzemionki (mikrokrzemionka) to z kolei produkt uboczny procesu metalurgicznego krzemu w elektrycznym piecu łukowym. Ze względu na wysoką aktywność pucolanową jest stosowany w betonach o wysokiej wytrzymałości. Z drugiej strony, jest też produktem ekspansywnym, a przy ograniczonej wydajności produkcyjnej nie może być stosowany jako substytut klinkieru portlandzkiego.
Obiecujące materiały SCM
Spośród różnorodnych materiałów typu SCM, mających na celu zmniejszenie zużycia zwykłego cementu, niezwykle obiecujące są kalcynowane iły, zwłaszcza w połączeniu z wapieniem. Dostępne w wystarczająco dużych ilościach stanowią realny potencjał do zastąpienia części cementu portlandzkiego. Wśród glinów najbardziej odpowiednim w omawianym zastosowaniu jest kaolinit – szeroko dostępny w środowiskach równikowych i subtropikalnych. Aktywność pucolanową kaolinitu uzyskuje się po kalcynacji w temperaturze od 600 do 800°C.
Cementy aktywowane alkaliami
Cementy aktywowane alkaliami charakteryzują się dużą zawartością fazy wiążącej glinokrzemianów, które nie reagują z wodą (lub tylko w niewielkim zakresie). Jednak ze względu na dużą zawartość substancji amorficznych hydrolizują i skraplają się po umieszczeniu w środowisku alkalicznym, tworząc trójwymiarowe struktury polimerowe, które mają zdolność przenoszenia obciążeń.
Cementy aktywowane alkaliami konkurują z cementem portlandzkim pod względem kosztów, wydajności oraz mniejszej emisji CO2. Ponadto okazały się one bardziej trwałe i zdolne do recyklingu przemysłowych ilości produktów ubocznych i odpadów. Głównymi stosowanymi materiałami są: żużel wielkopiecowy, żużel stalowniczy, metakaolin, popiół lotny, glinki kaolinitowe.
Cement portlandzki bogaty w belit
Kluczową różnicą w nowoczesnym cemencie portlandzkim i cemencie produkowanym ponad sto lat temu jest stosunek alit/belit. W cemencie portlandzkim bogatym w belit zawartość belitu wynosi ponad 50%. Taki cement nie tylko obniża wydzielanie ciepła, lecz także wykazuje doskonałą urabialność, lepsze właściwości mechaniczne i trwałość. Jest również bardziej odporny na siarczany i chlorki, ma wyższą wytrzymałość końcową w porównaniu z materiałem tradycyjnym.
Cement bogaty w belit jest wytwarzany w tym samym procesie co portlandzki, ale z mniejszą ilością wapienia w surowej mieszance. Do jego wad należy zaliczyć mniejszy skurcz suszenia i opóźniony przyrost wytrzymałości. Redukcja emisji wynosi w tym przypadku zaledwie ok. 10%.
Cement sulfoglinianowy wapnia
Cement na bazie sulfoglinianu wapnia zawiera wysoką ilość tlenku glinu. Do produkcji niezbędne są: boksyt, wapień i gips, które miesza się razem w piecu obrotowym. Cementy tego typu zostały opracowane w Chinach i zyskały na znaczeniu w późnych latach siedemdziesiątych.
Dzięki zastosowaniu takiej mieszanki można ograniczyć ilość wapienia w piecu, co – w porównaniu z cementem portlandzkim – nie tylko przynosi korzyści w postaci zmniejszenia energii cieplnej (do 25%), lecz także obniża CO2 (do 20%). Jako surowce do produkcji cementów sulfoglinianowych mogą być wykorzystywane odpady przemysłowe.
Cement na bazie magnezu
Spoiwa magnezjowe otrzymywane są z wapieni dolomitowych wypalanych w temperaturze 800–900°C w obecności chlorku lub siarczku magnezowego. W wyniku tego procesu otrzymuje się tlenek magnezu MgO, który w połączeniu z rozpuszczonym w wodzie chlorkiem magnezu (MgCl2) nazywany jest cementem Sorela.
Spoiwo magnezjowe po związaniu tworzy twardą i odporną na czynniki zewnętrzne powłokę, ale jego dużą wadą jest przyczynianie się do korozji stali. Obecnie w Polsce nie stosuje się spoiwa magnezjowego w budownictwie.
Do produkcji cementów magnezowo-węglanowych wykorzystywane są materiały uzupełniające (np. żużel, popiół lotny, pyłu krzemionkowy, popiół ściekowy, odpady kopalniane), a także brucyt i różne przyspieszacze. Powodem niewielkiej przydatności tej technologii spoiw jest niedobór surowca – główne źródło MgO to kalcynacja magnezytu, który jest minerałem rzadkim w porównaniu z węglanem wapnia. Ponadto podczas tej reakcji wytwarzana jest ogromna ilość CO2.
Z drugiej zaś strony proces wiązania magnezji pochłania CO2, co mimo wszystko przyczynia się do zmniejszenia jego ogólnej emisji.
Ciekawe podejście do produkcji cementów na bazie magnezu dotyczy zastosowania skał krzemianowo-magnezowych. Proces wytwarzania węglanu magnezu z krzemianów magnezu jest stosunkowo neutralny pod względem emisji CO2.
Nadal jednak trwają prace nad opatentowaniem produkcji tlenku magnezu z naturalnych skał w sposób energooszczędny, możliwy do wytworzenia na skalę przemysłową.
Karbonatyzowany cement krzemianowo-wapniowy
Krzemiany wapnia można utwardzać zarówno przez karbonatyzację, jak i hydratację. Częściowe utwardzanie karbonatyzacją jest już stosowane w niektórych wytwórniach prefabrykatów betonowych, co zwiększa ich wytrzymałość w porównaniu z utwardzaniem wilgotnym.
Rozwój specjalnej technologii karbonatyzacji klinkieru krzemianowo-wapniowego wciąż postępuje poprzez ulepszenie procesu nasycania dwutlenkiem węgla bez nadmiernego zużycia energii.
Do zalet należy zaliczyć niższą temperaturę syntezy tych klinkierów (ok. 1200°C) w porównaniu do spiekania cementu tradycyjnego, co przyczynia się do obniżenia o 30% emisji CO2. Cement krzemianowo-wapniowy wykazuje również wyższą wytrzymałość, a do jego produkcji zużywa się znacznie mniej wody.
Wytworzony cement może być utwardzany tylko w stosunkowo czystym gazowym CO2, o kontrolowanej temperaturze i wilgotności względnej. Wymaga to pewnych modyfikacji w komorach utwardzania i wiąże się z dodatkowymi kosztami.
Oprócz tego, betony zawierające ten rodzaj cementu nie są w stanie w odpowiedni sposób zabezpieczyć stali przed korozją i mogą być stosowane do betonu niezbrojonego.
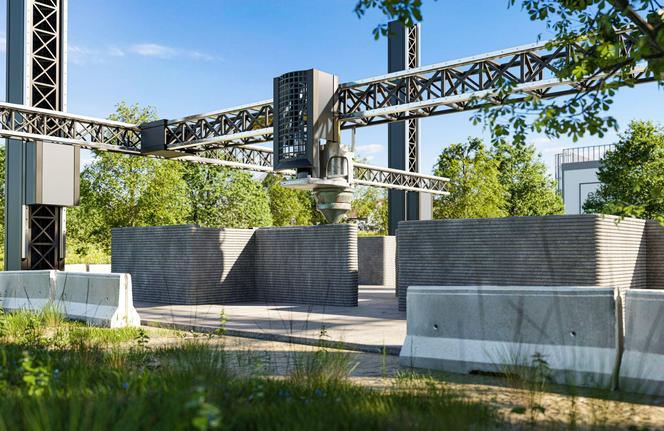
i
Zrównoważony rozwój w przemyśle cementowym
Czynnikami, które mają ogromny wpływ na zagadnienia zrównoważonego rozwoju w przemyśle cementowym, a w szczególności na emisję CO2, są decyzje polityczne. Opodatkowanie emisji CO2 to strategia, która ma zniechęcać do stosowania konwencjonalnego cementu.
Rosnące koszty produkcji z założenia powinny mobilizować inżynierów do poszukiwania nowych rozwiązań konstrukcyjnych lub materiałów. Poza tym, tego typu działania mogą teoretycznie zapewniać rządom dodatkowe fundusze, np. na zapewnienie specjalnej infrastruktury do walki ze zmianami klimatycznymi.
Obiecująco zapowiadają się także postępy we wdrażaniu technologii druku 3D, które zdaniem wielu mogą wprost zrewolucjonizować branżę budowlaną. Ponadto coraz większą popularnością cieszą się konstrukcje prefabrykowane. Precyzyjny sposób wytwarzania takich komponentów przyczynia się do zmniejszania marnotrawstwa materiałów, w szczególności betonu.
Uwagę należy zwrócić również na kwestie optymalizacji transportu, a także rozpowszechnienie technologii BIM, która pozwala na efektywne planowanie i zarządzanie.
Potencjał betonu niskoemisyjnego, zwłaszcza alternatywnych cementów, można w pełni zrealizować jedynie poprzez dalsze szczegółowe badania i określenie ich charakterystyki za pomocą nowoczesnych technologii. Prawdopodobnie w przyszłości istotną rolę odegra również ustalenie standardów i wytycznych oraz odpowiednia edukacja.
W ostateczności sukces na drodze do zrównoważenia produkcji cementu zależy od ekonomicznej, strategicznej wizji planowania, zarówno przedsiębiorców działających w branży cementowej, jak i rządu. Wprowadzenie programów zachęcających do produkcji ekologicznych wyrobów (związanych z redukcją emisji CO2) oraz przesunięcie nacisku na długofalowe korzyści, mogą wkrótce zaowocować dynamicznym rozwojem i rozpowszechnieniem alternatywnych spoiw.